AC Capacitor Replacement Guide
Welcome to Bryant, your trusted source for air conditioning systems. Here, we provide a comprehensive overview of AC capacitors, signs of a failing air conditioner capacitor, the step-by-step process for AC capacitor replacement and the reasons to work with a Bryant dealer for AC capacitor replacement. Read on to discover everything you need to know about AC capacitor replacement.
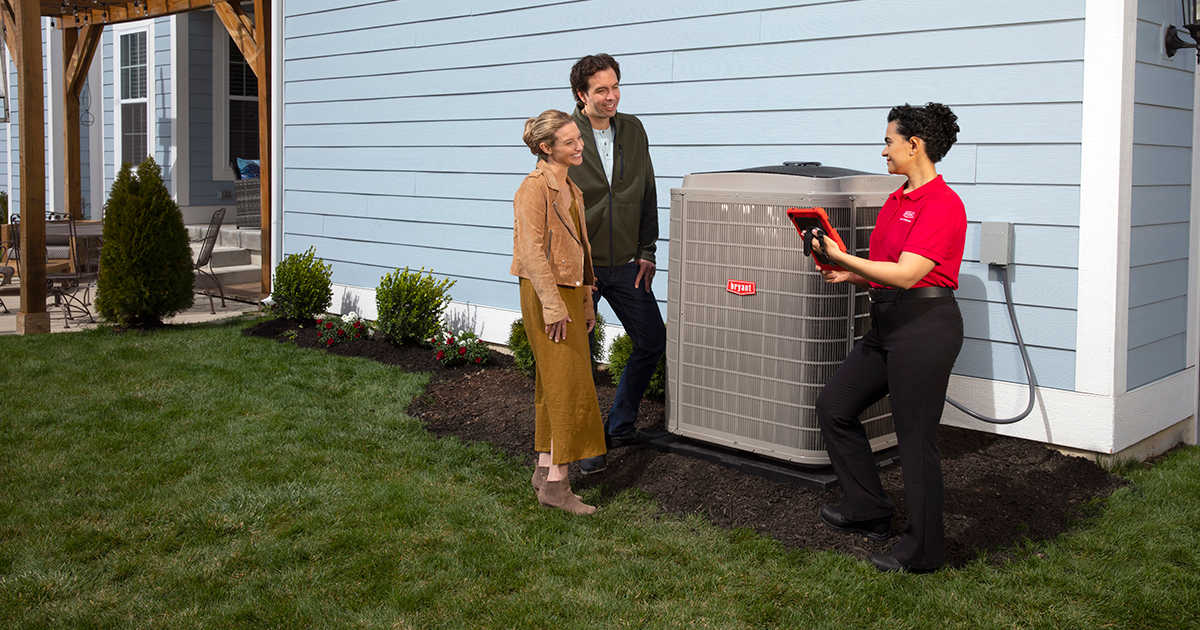
What Is An AC Capacitor?
An AC capacitor is a crucial electrical component in air conditioning systems that helps start and run the motor of the compressor and the fan. It stores electrical energy and releases it as needed to provide a boost to the motor during startup and to keep it running efficiently.
What Does A Capacitor Do?
There are two main types of capacitors in an AC unit: start capacitors and run capacitors. The start capacitor provides a temporary burst of energy to the motor during startup, while the run capacitor ensures smooth, continuous operation by supplying power to the motor throughout the cycle. Without a properly functioning capacitor, the motor may not start, may run inefficiently, or could overheat. Over time, capacitors can wear out or fail due to age or wear, leading to poor performance or system failure. Replacing a faulty capacitor is essential to maintain the overall efficiency and reliability of your air conditioning system.
Signs of a Failing Air Conditioner Capacitor
Recognizing the signs of a failing AC capacitor is crucial for maintaining your air conditioning system's efficiency and longevity. Symptoms indicating capacitor failure can manifest in various ways, including an unusual humming noise from the unit, frequent tripping of the circuit breaker, or the AC unit failing to start.
Additionally, if your air conditioner experiences a noticeable decrease in cooling performance or exhibits inconsistent airflow, these may also be indicators of capacitor issues.
Understanding the potential causes of capacitor problems can help you prevent future failures. Capacitors may fail due to overheating, prolonged use in high temperatures, or age-related wear and tear. Power surges and poor installation practices can also contribute to capacitor damage, leading to costly repairs or replacements.
Timely AC capacitor replacement is essential to avoid further damage to your HVAC system. Neglecting a failing capacitor can result in strain on other components, such as the compressor, leading to more extensive and expensive repairs. By addressing capacitor issues promptly, you not only ensure your system operates efficiently but also extend its overall lifespan. Regular AC maintenance checks can help identify problems early, allowing you to replace any faulty air conditioner capacitors and keep your home comfortable.
Step-By-Step Process To AC Capacitor Replacement
By following these detailed steps, a professional HVAC technician ensures that the capacitor is replaced correctly and safely, maintaining the overall health and efficiency of your AC system.
Step 1: Power Off the System
The technician will turn off the power to the HVAC system by flipping the circuit breaker that controls the air conditioning unit. Using a multimeter, the technician will verify that there’s no voltage running to the capacitor or any other electrical component before proceeding.
Step 2: Access the Capacitor
The technician will locate the capacitor in the outdoor condenser unit. Most systems have the capacitor inside the control panel of the outdoor unit. Using a screwdriver or appropriate tool, the technician will remove the screws or bolts securing the access panel of the condenser to access the capacitor.
Step 3: Discharge the Capacitor
Capacitors can hold a charge even after power has been turned off. The technician will take extra precautions to discharge the capacitor. The technician will use an insulated tool, like a screwdriver with a rubber handle, to safely short across the capacitor’s terminals (C, Fan, and Herm). This will safely discharge any remaining electrical charge from the capacitor.
Step 4: Verify the Capacitor’s Condition
The technician may use a capacitor tester or multimeter to check the capacitor's microfarad rating (µF) and determine whether it is still functioning correctly. If the capacitor is out of spec or showing signs of damage, it will need replacement. Any visual damage, such as bulging, leaking, or burnt spots on the capacitor, will indicate a failed part that needs replacing.
Step 5: Record Wiring Connections
Before removing any wires, the technician will label each connection to the capacitor, ensuring the new capacitor is connected properly. They may also take a picture of the wiring configuration to ensure accuracy. The technician will confirm the voltage and capacitance (µF) rating on the existing capacitor to ensure the replacement matches.
Step 6: Remove the Old Capacitor
The technician will carefully disconnect the wires from the old capacitor, making sure to handle the wires gently and avoid damaging the connections. If there are screws or brackets holding the capacitor in place, the technician will remove them to free the old capacitor.
Step 7: Install the New Capacitor
The technician will select a replacement capacitor that matches the specifications of the old one, including the voltage and capacitance rating. The technician will mount the new capacitor in the same position as the old one, securing it with the appropriate brackets or fasteners. The technician will reconnect the wires to the new capacitor, ensuring each wire is connected to the correct terminal (C, Fan, and Herm).
Step 8: Double-Check Connections
Before proceeding, the technician will double-check the connections to ensure they are secure and correct. Proper wire placement is essential for safe and efficient operation.
Step 9: Test the New Capacitor
The technician will turn the power back on at the breaker and check for any immediate issues or irregularities. They will turn on the AC unit and observe the system's operation. They’ll listen for proper compressor and fan operation, as well as check the temperature to ensure that the system is cooling effectively. The technician may use a multimeter to check the voltage across the terminals of the new capacitor to confirm it’s functioning correctly.
Step 10: Reassemble the Unit
Once the new capacitor is installed and functioning properly, the technician will replace the access panel and secure it with screws. Any tools or debris will be cleaned up and removed from the area.
Step 11: Final System Check and Customer Instructions
The technician will perform a final check on the entire system, ensuring everything is working as it should. They will explain to the homeowner what was done, any potential signs to look for (such as if the capacitor fails again), and provide maintenance tips for extending the life of the HVAC system.
Step 12: Documenting the Service
The technician will document the work performed, including details about the capacitor replaced, model/serial numbers, and any other relevant information. The technician will finalize the service report, process payment, and may offer additional recommendations for future maintenance or repairs.
AC Capacitor Cost
The cost of replacing an AC capacitor typically ranges from $100 to $400, depending on factors like the type of capacitor, your location, and whether you hire a professional for the job. The capacitor itself usually costs between $20 to $100, but labor charges for the replacement can add another $75 to $300. Consult your local Bryant dealer for a precise AC capacitor cost.
Connect With A Bryant Dealer On AC Capacitor Replacement
Working with a Bryant Factory Authorized Dealer for AC capacitor replacement (or any HVAC work) offers several advantages, especially when it comes to ensuring quality, efficiency, and longevity of your system. Here are some key reasons why it’s beneficial to work with a Bryant Factory Authorized Dealer for capacitor replacement:
Proper Diagnosis and Solution
Bryant dealers have access to diagnostic tools and training specifically designed for HVAC units. If the capacitor is malfunctioning, they can assess whether it’s the sole issue or if there are other underlying problems, such as compressor or fan motor issues. Bryant Dealers will make sure the new capacitor matches the specifications required for your particular model, which is critical for maintaining efficiency and reliability.
Professional Expertise
Professional installation using the correct parts and techniques increases the likelihood that your AC system will operate smoothly for years. Bryant dealers are focused on long-term results rather than quick fixes.
Access to Warranty
If your Bryant system is still under warranty, a Bryant dealer can help with warranty claims. Additionally, they’ll ensure that the capacitor replacement (and any other repairs) are documented properly, so you’re not left with an unexpected repair cost.
Service Plans
Bryant Dealers often offer maintenance agreements that can help keep your system running efficiently and prevent future breakdowns. With regular maintenance, your system’s lifespan can be extended, and the chances of needing emergency repairs are reduced.
Professional Standards and Customer Service
Bryant Factory Authorized Dealers are required to be licensed and insured, which ensures you’re working with professionals who meet industry standards for safety and quality. If any issues arise during or after the repair, you have the peace of mind knowing you’re covered.
Bryant dealers are focused on providing excellent customer service. They are likely to offer personalized recommendations and take the time to explain what was done during the repair, ensuring you're fully informed about your system’s needs.
Energy Efficiency and Performance
Bryant dealers can also offer advice on improving the energy efficiency of your system. When you replace the capacitor, it’s an ideal time to check for other maintenance issues that could improve the performance and efficiency of your AC, saving you money on cooling bills.
Expertise with Bryant Systems
Bryant dealers are trained specifically in Bryant systems. They have a deep understanding of the Bryant’s models, components, and performance specifications. This makes them well-equipped to handle repairs and replacements with a high level of precision. As a Factory Authorized Dealer, the technician will have been trained and certified by Bryant, ensuring they follow best practices when diagnosing and servicing the unit.
Access to Genuine Bryant Parts
A Bryant dealer can source genuine Bryant capacitors, which are designed to work seamlessly with your Bryant HVAC system. Using OEM (original equipment manufacturer) parts ensures optimal performance and extends the lifespan of your system. Using genuine parts also helps preserve your system’s warranty. Many HVAC systems, including Bryant, require the use of OEM parts for warranty coverage to remain intact.
Connect With Your Local Bryant Dealer for AC Capacitor Replacement
In short, working with a Bryant dealer for your AC capacitor replacement ensures that you're getting high-quality, expert service tailored to your HVAC system. It’s an investment in both the immediate and long-term health of your air conditioning system. Schedule an appointment with your local Bryant dealer today.
Learn More About Air Conditioners
- Explore Bryant air conditioners
- Learn about types of air conditioners and how does air conditioning work
- Get in the know on air conditioning service
- Find out what is a split AC unit and an inverter air conditioner
- Explore AC installation and AC replacement
- Learn the ins and outs of a central air conditioner
- Understand AC maintenance and AC tune ups
- Discover the factors in choosing the best air conditioner and what size air conditioner you need
- Explore wall AC and garage AC unit options
- Understand the definition of SEER2, EER2, and BTU
- Read our guides to AC parts and air conditioning systems
- Get help with an AC not working, mold in air conditioner, AC leaking water, AC smells, or AC not blowing cold air
- Explore the ins and outs of AC drain lines
- Learn about AC refrigerant, including R-22 refrigerant, R-410A refrigerant and R-454B refrigerant
- Find out how long do AC units last?
- Learn how to clean AC coils , how to clean air conditioners, and how to perform air filter replacement
- Discover the difference in a heat pump vs air conditioner
- Find out what temperature to set air conditioner in summer